Chelsea Leu, California Magazine
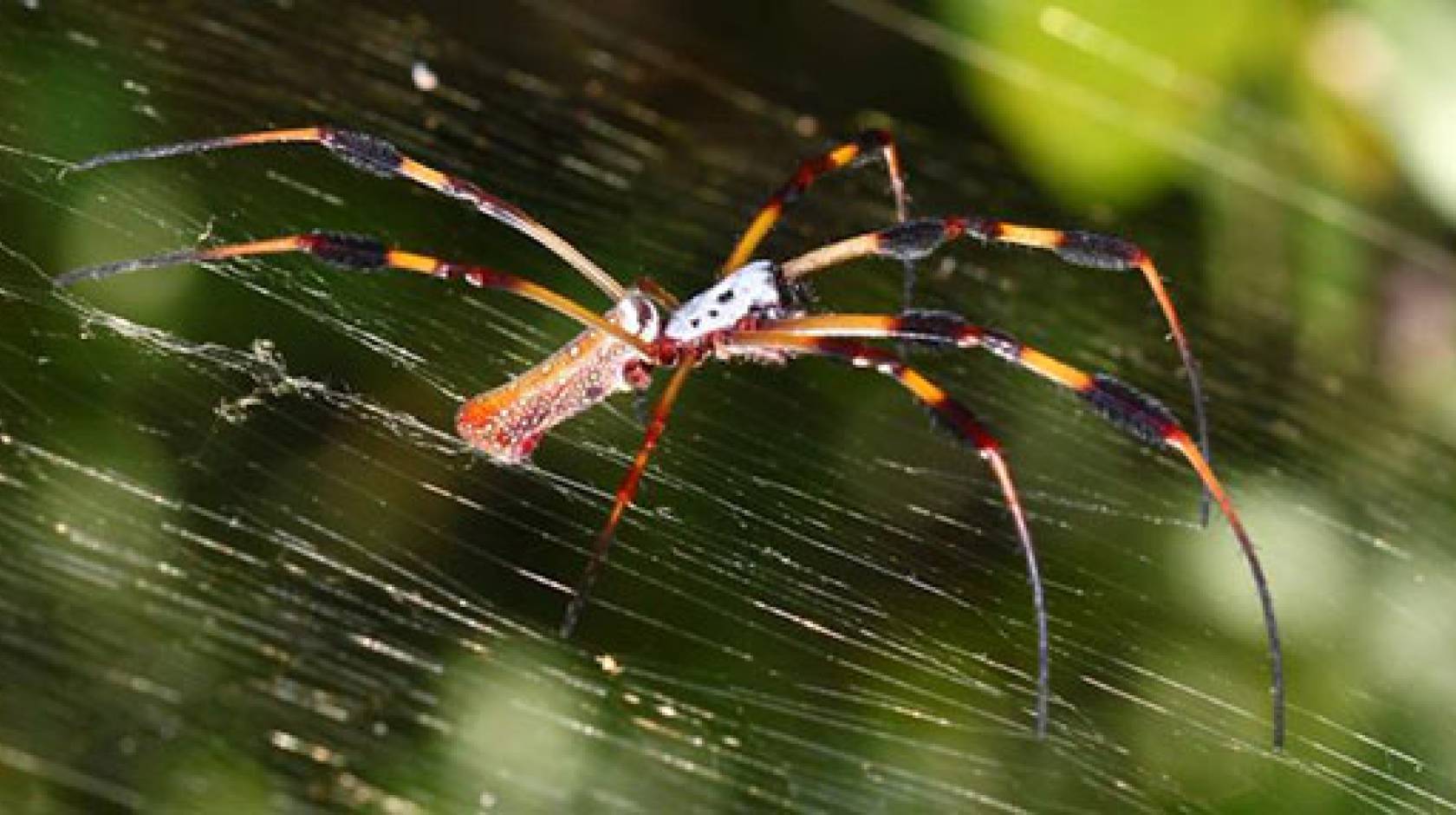
In the beginning, David Breslauer’s office was infested with spiders — lurking in the corners, hunkered down on their webs, crawling up his arms. “I had one right above my desk, and it pooed on my computer like a pigeon,” he says. And these were large, long-legged beasties, too: Nephila clavipes, an orb-weaving species commonly used in scientific studies.
Which is, of course, exactly why they were roaming free. Breslauer, who got his bioengineering Ph.D. from UC Berkeley in 2010, is in the business of making silk — specifically, spider silk. He and his partners, two UC San Francisco Ph.D.s, have founded Bolt Threads, a company that is now making synthetic spider silk that’s chemically identical to the natural stuff, and they’ve built up an innovative process to produce it on an industrial scale. To pull this off, the three had to become intimately acquainted with the material they were trying to mimic. “We tried building spider cages, but these spiders were large, and they needed a lot of space to build their webs,” Breslauer says. So in 2011, their office became the cage. “I habituated to them surprisingly quickly,” he says, though the company later moved to its current headquarters in Emeryville.
Spider silk, like all silk, is a type of protein. The material is highly valued not only for its famed strength but also because natural spider silk comes in a variety of forms. “Each spider spins about seven different types of silk,” Breslauer says. They produce an incredibly soft variety for egg wrapping; another type, called flagelliform silk, is incredibly stretchy like spandex. These varieties have evolved for spiders’ specific ecological needs, and also happen to be qualities we’d like in our clothing, too. (Spider silk Spanx, anyone?) Accordingly, scientists have been attempting to synthesize these silks for decades. But the process is surprisingly finicky, and no one’s come up with a good way to mimic it on a commercially viable scale.
Until now.